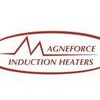
Magneforce has the experience necessary to specify the induction heater, induction coil, control method, and ancillary equipment best suited to your operation. Heat Station induction heaters are currently used in industrial, medical, and scientific processes.
These include brazing of tools, tubes, and fittings, soldering connectors and terminals, heating inserts for hot pressing into plastics, shrink fitting of gears, rings, and bearings, preheating for welding and molding operations, melting, heat staking, cap sealing, extruder barrel heating, curing coatings and adhesives, heating catheter molds, annealing, stress relieving, and process heating applications.
These include brazing of tools, tubes, and fittings, soldering connectors and terminals, heating inserts for hot pressing into plastics, shrink fitting of gears, rings, and bearings, preheating for welding and molding operations, melting, heat staking, cap sealing, extruder barrel heating, curing coatings and adhesives, heating catheter molds, annealing, stress relieving, and process heating applications.
Services
The Heat Station 1500 B is a 1.5 kW induction heater with a built in output transformer. The Heat Station 1500 R features the output transformer on a 3-foot flexible cable. These medium frequency induction heaters operate in the 20-50 kHz range and provide fast and precise heating for soldering, brazing, heat staking, and catheter tipping operations.
The Heat Station 2500 R2 and Heat Station 2500 R2C are 2.5 kW induction heaters with an included remote output transformer attached to the power supply by means of a 6-foot flexible conduit. This conduit carries power and water cooling. These medium frequency induction heaters operate in the 20-50 kHz range and provide fast and precise heating for soldering, brazing, heat staking, and shrink fitting applications.
Controls are used to turn heating on and off, set power level, set heating time, set process temperatures and verify the heating process. Power can be changed on the fly during the heating cycle based on programmed times or temperature readings. Manual controls such as on/off or power control foot pedals, push button and timer stations, built in two stage time and power panels, or PLC connection cables are available.
Induction Heating systems require water cooling in order to remove the heat generated by electrical losses in the heating system. In particular, losses due to the very high amperages present in the induction coil. Magneforce offers Dynaux brand water recirculators which utilize vane pumps capable of producing water pressure to 80 psi and fan cooled radiators for heat removal.
Induction heating is used to heat metals to be joined until a brazing alloy which is placed inside or in proximity to the joint, along with a fluxing agent, melts and creates a bond between the metals. The ability of induction heating to provide a controlled heat input and heat pattern with consistency greatly reduces the skill level required to produce joints of good quality and appearance.
Reviews
Be the first to review Magneforce.
Write a Review